Fertigungsrichtlinien
SCHNEIDRICHTLINIEN FÜR ROHRE
Allgemein
Es besteht ein Unterschied zwischen Stahl- und Edelstahlrohren und Aluminiumrohren (siehe auch zwischen 2,5D (90°) schneiden und 3D muss speziell angefragt werden weil wir grundsätzlich 2,5D schneiden.
Stahl und Rostfreier Stahl
Für Stahl- und Edelstahlrohre (quadratisch und rechteckig) sollten die Radien wie folgt gezeichnet werden: - Außenradius = 2x Wandstärke (Der Wert '2' ist ein Durchschnittswert für die Größe der in der Norm genannten Radien). - Innenradius = 1x Wandstärke.
ALUMINIUM
Für Aluminiumrohre (quadratisch und rechteckig) sollten die Radien wie folgt gezeichnet werden:
- Außenradius > 0 bis 0,6mm Radius (spitzer Winkel)
- Innenradius = 0 mm Radius (spitzer Winkel)
Mayer Laserschneiden & Metall schneidet 2,5D. Dies bedeutet, dass sich die Schneidfläche senkrecht auf dem Material befindet (am Mittelpunkt ausgerichtet). Bei Rohren ist sie an der Ache des Rohres ausgerichtet. Einige Beispiele dazu werden später in dieser Anleitung gegeben. Die Software unserer Maschine wandelt selbstständig 3D-Schnittflächen in 2,5D-Schnittflächen.
Mögliche Wanddicken
- Aluminium (Rohr): bis zu 6 mm
- S355 (st.52): bis 10 mm
- Edelstahl Rostfrei: bis 6 mm
MÖGLICHE ABMESSUNGEN
- Rohrdurchmesser: mindestens Ø12,0 mm und maximal Ø240 mm.
- Quadrat-Rechteckrohr: mindestens viereckig 12x12 mm und maximal 200x200 mm.
Höchstgewicht des Produktes je Meter: 32 kg. Maximale per Laser zu schneidende Länge aus einem Stück: 5.800 mm. Für Aussparungen oder Bohrungen gilt ein Durchmesser von mindestens 0,7 x Materialstärke. Dies dient der Sicherstellung der Schnittqualität.
TOLRERANZEN
Die Toleranzen bei der geschnittenen Kontur, der Zentrierung der geschnittenen Kontur und bei der Gesamtlänge betragen +/- 0,5 mm/mtr. Die Toleranzen werden durch eine Reihe von Faktoren stark beeinflusst, wie zum Beispiel:
- Form- und Messtoleranzen bei Rohren und Kantteilen. Diese werden in den entsprechenden Normblättern (beispielsweise EN10219) beschrieben. Abweichungen bei den Maßen der Rohre und Kantteile haben einen unmittelbaren Einfluss auf die Zentrierung der geschnittenen Konturen.
- Maße und die Steifigkeit des Rohrs oder Kantteils. Kleine und schmale Kantteile sind flexibel und bewegen sich während des Laserschneidens stark in der Maschine. Hieraus können Abweichungen im Aufmaß und bei Schnittmustern entstehen.
- Wärmeeinbringung durch Konturen. Wenn in ein Rohr oder ein Kant Teil zahlreiche Konturen geschnitten werden, ergibt sich hieraus ein großer Wärmeeintrag und die Toleranzen können abweichen. Außerdem kommt es zu Verfärbungen des Materials.
- Abbrand Staub (Stab Spritzer im Rohrinneren) durch die Laserbearbeitung ist zu akzeptieren, wenn dies nicht gewünscht ist, muss das bei Anfrage, Bestellung speziell angefragt werden, Reklamationen werden nicht anerkannt.
Position der Schweißnaht
Bei der Beladung der Maschine werden die Kantteile willkürlich geladen (manchmal in einem kompletten Bündel). Dadurch ist es möglich, dass die Schweißnaht bei gleichen Produkten auf unterschiedlichen Seiten liegt.
Bei rechteckigen Rohren gibt es zwei Möglichkeiten für die Position der Schweißnaht, sowohl an den kurzen als auch an den langen Seiten. Wir wissen nicht im Voraus, wo sich diese befindet, daher ist es wichtig, dass bei rechteckigen Rohren an beiden Stellen eine Schweißnahtposition angegeben wird.
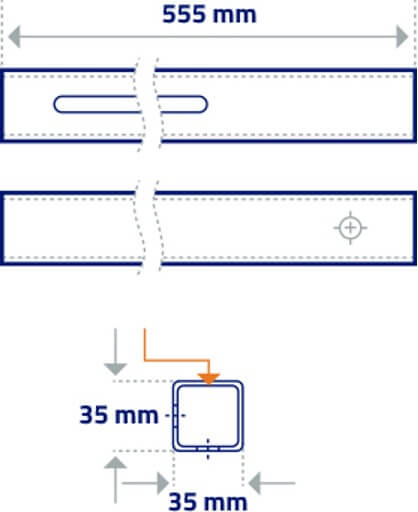
Beispiel: Der orangene Pfeil steht für die Position der Schweißnaht
Spat an der Innenseite des Rohrs/Kantteils
Das flüssige Material, das sich während des Laserschneidens an die gegenüberliegende Innenseite heften kann, wird auch als Spat bezeichnet. Die Menge an Spat ist abhängig von mehreren Faktoren:
- Innendurchmesser des Rohrs/Kantteils Je größer der Durchmesser ist, desto kleiner ist die Menge an Spat.
- Wanddicke vom Rohr/Kantteil Je größer die Wanddicke, desto größer ist die Spat-Menge.
- Innenfläche vom Rohr/Kantteil Ein glatt/fettiges Rohr bzw. ein glatt/fettiges Kantteil ist gegenüber Spat-Haftung unempfindlicher als ein roh/trockenes Rohr bzw. Kantteil.
Gravieren
Mayer Laserschneiden graviert nur funktional zwecks Positionierung oder Identifizierung. Blindlöcher werden automatisch als Gravur erkannt. Wenn gewünscht, kann Mayer Laserschneiden eine Schnittkontur in eine Gravur umwandeln oder wenn in der Step Zeichnung die Kontur 0,2mm tief gezeichnet wurde.
2,5D-Laserschneiden
Mayer Laserschneiden schneidet 2,5D. Dies bedeutet, dass sich die Schnittfläche senkrecht auf dem Material befindet (am Mittelpunkt ausgerichtet). Die Software von Mayer Laserschneiden konvertiert selbstständig 3D-Schnittflächen in 2,5D-Schnittflächen. Daher ist es möglich, dass ein Produkt etwas anders geschnitten als gezeichnet wird. Damit Sie sich hiervon einen Eindruck machen können, beachten Sie bitte folgende Beispiele:
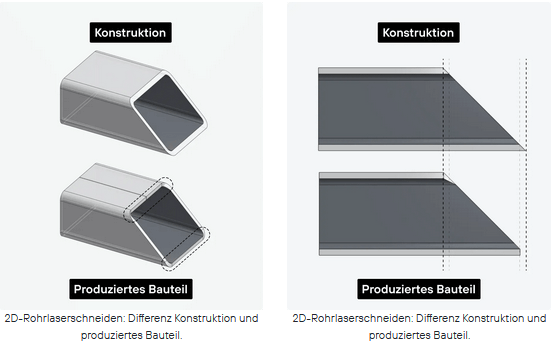
Beispiel – 2,5D-Zeichnung
2,5D geschnittene Löcher im Rundrohr
Erläuterung Löcher in Rundrohren werden standardmäßig senkrecht zum Material (am Mittelpunkt ausgerichtet) geschnitten. Entsprechend werden die Löcher anders geschnitten als gezeichnet. Zylindrisch gezeichnete Löcher (blaue Linien in der Abbildung) werden ellipsenförmig geschnitten (orangene Schnittlinien in der Abbildung). Der Durchmesser eines runden Lochs, gemessen am Innendurchmesser des Rundrohres, entspricht dem Durchmesser des gezeichneten Lochs. Der Durchmesser des Lochs, gemessen am Außendurchmesser des Rohres, ist größer und ellipsenförmig. Diese Löcher sind u.a. nicht für Schraubgewinde geeignet.
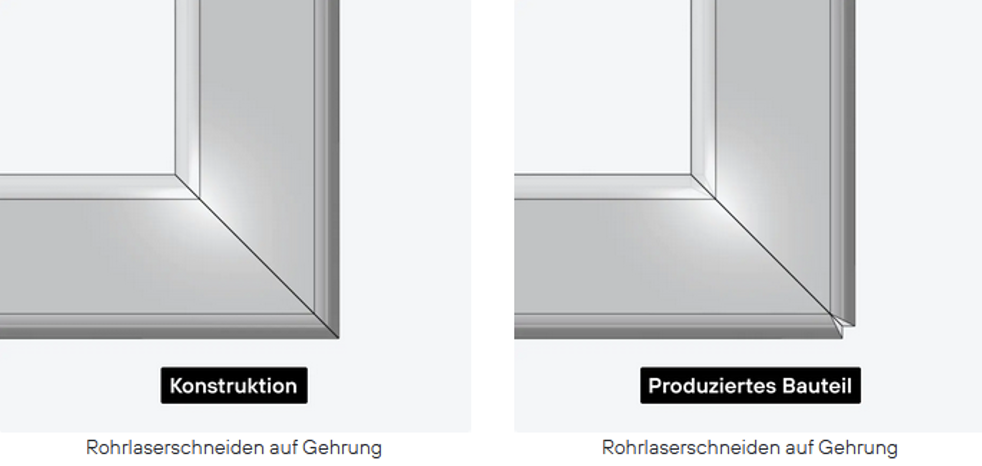
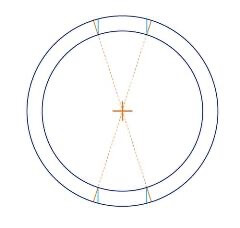
Beispiel – Zeichnung
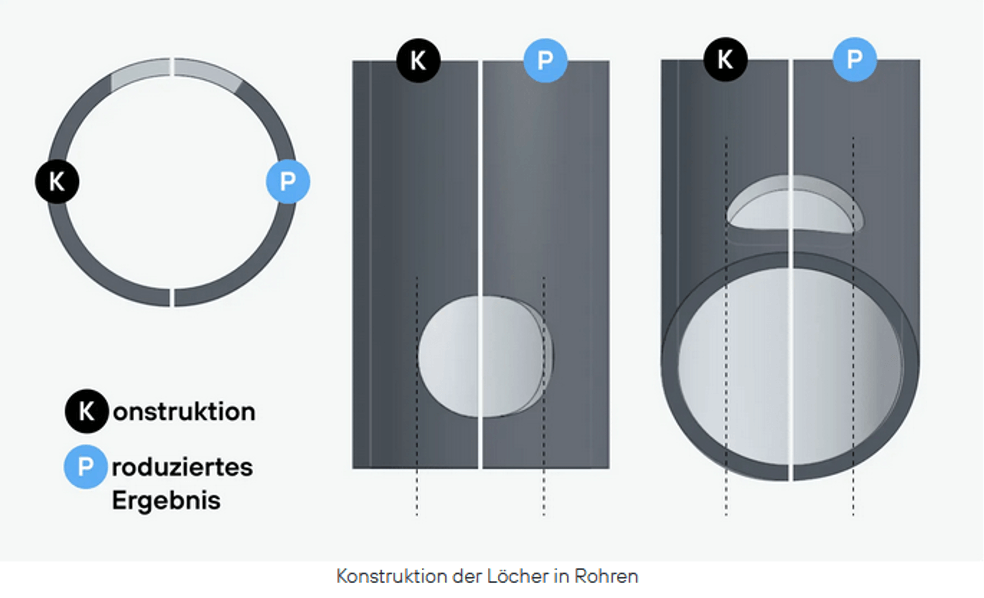
Beispiel - Zeichnung
Falls ein solches Loch doch zylindrisch geschnitten werden soll, müssen wir hierüber innerhalb von 24 Stunden nach Auftragsvergabe informiert werden. Dies sollte in Form einer eindeutigen pdf-Zeichnung geschehen, der eindeutig zu entnehmen ist, welche Bearbeitungen zylindrisch zu schneiden sind.
AUFGEPASST! Der Durchmesser zylindrischer Löcher in Rundrohren ist beschränkt; sie können nicht größer werden als circa 0,5 x Rohrdurchmesser.
2,5D-Laserschneiden auf Gehrung
Mayer Laserschneiden schneidet 2,5D. Dies bedeutet, dass sich die Schneidfläche senkrecht auf dem Material befindet (am Mittelpunkt ausgerichtet). Bei Produkten, die auf Gehrung gezeichnet sind, hat das zur Folge, dass in den äußeren Ecken eine Furche entsteht (siehe Abbildungen unten). Häufig werden diese Furchen während des Schweißens gefüllt.
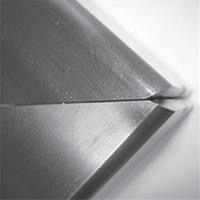
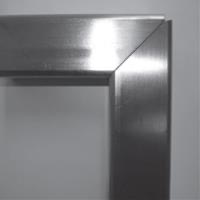
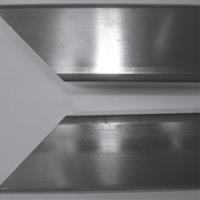
Beispiel - Kantteile
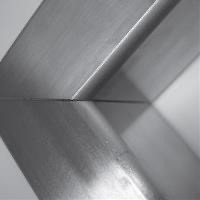
Beispiel - Kantteile
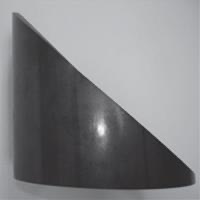
Beispiel - Rohre
Die Methoden für das Rohrlaserschneiden: 2,5D-, 3D- und zylindrisches Schneiden Beginnen wir mit dem verschieden Rohlaserschneidtechniken. Wir schneiden Rundrohre und Vierkantrohre standardmäßig in 2,5D, auch unter der Bezeichnung 90°-Rohrlaserschneiden bekannt. Das bedeutet, dass der Schnitt im rechten Winkel zum Material verläuft.
Eine Bearbeitung kann auch in 3D erfolgen. Dies ist bis zu einem Winkel von maximal 45° möglich, da der Laserschneidkopf bei diesem Schneideverfahren bis zu 45 Grad kippen kann. Der Vorteil dieser Art des Schneidens ist die Tatsache, dass die verschiedenen Teile Ihres Endprodukts nahtlos ineinander passen.
Zusätzlich kann mittels 3D-Laserschneiden ein abgeschrägtes Loch geschnitten werden, in das ein Bolzen versenkt werden kann. Sie möchten Ihr Rundrohr oder Vierkantrohr in 3D laserschneiden lassen? Dann müssen Sie dies separat uns mitteilen, weil bei uns das automatisch in 2,5D konvertiert wird. Dadurch ist es möglich, dass Ihr Design anders geschnitten wird, als Sie gezeichnet haben. So kann es beispielsweise vorkommen, dass Schnittlinien nicht korrekt konvertiert werden und die Verbindungen zwischen den Rohren somit nicht nahtlos sind (siehe Beispiel unten). 3D Gehrungsschnitte sind in der Zuschnitts länge immer circa 1mm je Gehrungsschnitt kürzer, weil der spitzen Winkel beim Schneiden abgerundet wird. Dies wird unsererseits nicht als Grund zur Reklamation angesehen / akzeptiert.
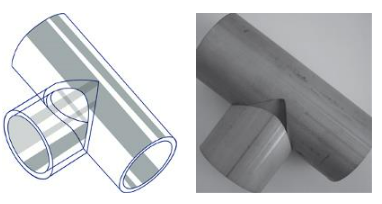
3D-Zeichnung im 2,5D-Laserschnitt
Es gibt auch ein anderes Schneideverfahren, nämlich zylindrisches Schneiden. Dies wird auch als XY-Schneiden bezeichnet: Der Laserschneidkopf folgt der Kontur des Lochs. Diese Art des Schneidens ähnelt dem Anfertigen eines Bohrlochs. Wenn Sie zylindrische Bohrungen in Ihrem Design wünschen, teilen Sie uns dies bitte anhand einer übersichtlichen PDF-Zeichnung mit. Diese muss innerhalb von 24 Stunden nach Auftragserteilung bei uns unter info@mayer-laserschneiden.de mittgeteilt werden.
Hinweis: Bitte beachten Sie, dass der Durchmesser eines zylindrischen Lochs in Rundrohren maximal das 0,5-fache des Rohrdurchmessers betragen darf.
Radius an Rohrecken zeichnen
Dann sind wir nun beim Zeichnen der Ecken von quadratischen oder rechteckigen Rohren, mit anderen Worten, von Vierkantrohren, angekommen. Es hängt von der Art des Materials ab, welche Maße Sie zum Zeichnen des Innen- und Außenradius Ihres Vierkantrohres verwenden sollten. Der Außenradius ist der wichtigste Radius damit Rohr Konstruktionen sauber Maß genau sind.
Wie der nachfolgenden Übersicht zu entnehmen ist, gelten für die verschiedenen Materialarten unterschiedliche Richtlinien. Wo Edelstahl und Stahl abgerundete Ecken und damit einen Radius haben, zeichnet sich ein Aluminiumrohr durch die scharfen Ecken aus.
Innenradius | Außenradius | |
---|---|---|
Edelstahl | 1 x die Wandstärke | 1,8 bis 2,2 x Wandstärke |
Stahl | 1 x die Wandstärke | 1,8 bis 2,2 x Wandstärke |
Aluminium | 0 mm Radius | 0 bis 0,6 mm Radius |
Darüber hinaus können Sie eine zusätzliche „Brücke“ zeichnen, um den erforderlichen vollen Umfang zu erhalten (siehe Abbildung).
Verbindungen von Rohren
Verbindungen von Rohren führen häufig zu Problemen, wenn diese 3D gezeichnet sind. Unser Programm konvertiert die Schnittlinien nicht in jedem Fall korrekt, wodurch die Verbindung der Rohre untereinander nicht „nahtlos“ ist. In einigen Fällen kann dies intern gelöst werden, aber in der Regel ist es erforderlich, neue Zeichnungen anzufertigen. Betrachten Sie bitte das unten stehende Beispiel für eine 3D-Zeichnung mit dem Produkt als Ergebnis und ein Beispiel einer Rohrverbindung, die vollständig 2,5D gezeichnet ist.
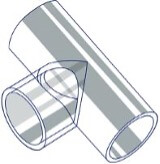
Beispiel – 3D-Zeichnung
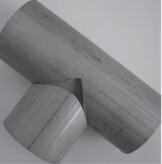
Beispiel – Tatsächliches Produkt
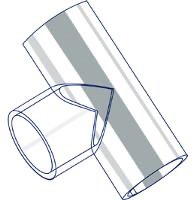
Beispiel – 3D-Zeichnung
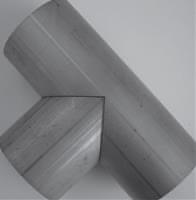
Beispiel – Tatsächliches Produkt
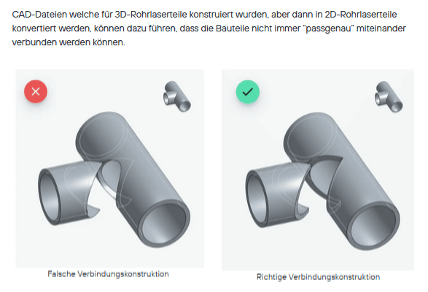
AUFGEPASST!
Jeder Auftrag ist für uns einmalig. Daher ist es auch bei wiederkehrenden Produkten wichtig, dass beispielsweise die Position der Schweißnaht oder Gravuren erneut angegeben werden.
Art des Zeichnens
Art des Zeichnens Wenn eine Bearbeitung nahe der Wandstärke durchgeführt wird, ist es wichtig, dass die Bearbeitung an dieser Stelle mindestens 0,1 mm davon entfernt ist. (siehe Abbildung)
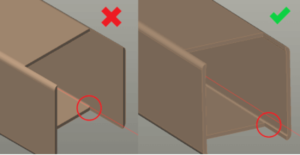
Beispiel- Mindestabstand
Um die bestmögliche Schneidqualität an den Ecken zu erhalten, empfehlen wir die Eckaussparung wie folgt zu zeichnen. (siehe Abbildung)
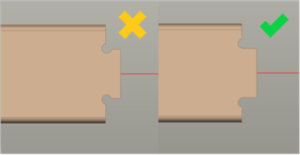
Beispiel - Zeichnung Rohre
Blindnietmuttern
- Material Blindnietmutter: Edelstahl und verzinkter Stahl;
- Nur möglich bei quadratischen oder rechteckigen Rohren;
- Nur ein Typ von Blindnietmutter pro Auftrag;
- Flansch darf Radius nicht überschreiten.
Die untenstehende Tabelle zeigt, bei welcher Wandstärke welcher Typ von Blindnietmutter montiert werden kann:
Typ Wanddicke (mm)
0,5 | 1 | 1,5 | 2 | 2,5 | 3 | 3,5 | 4 | |
M4 | ✔ | ✔ | ✔ | ✔ | - | - | - | - |
M5 | ✔ | ✔ | ✔ | ✔ | ✔ | ✔ | - | - |
M6 | ✔ | ✔ | ✔ | ✔ | ✔ | ✔ | - | - | M8 | ✔ | ✔ | ✔ | ✔ | ✔ | ✔ | - | - |
✔= Blindnietmutter möglich
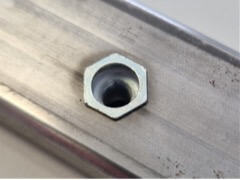
* Nur in verzinktem Stahl erhältlich
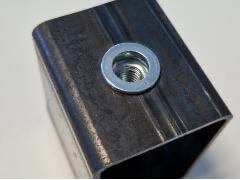
* Nur in verzinktem Stahl erhältlich
Größe der Bohrung | |
---|---|
Typ, Große (B) | |
M4 | 6 mm |
M5 | 7 mm |
M5 | 9 mm | M5 | 11 mm |
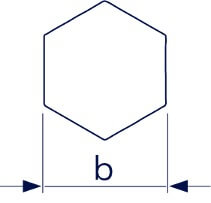
Größe der Bohrung
Minimale Rohrgröße
Blindnietmutter auf einer Seite | |
---|---|
Typ, Mindesthöhe (H) | |
M4 | 19 mm |
M5 | 22 mm |
M5 | 24 mm | M5 | 26 mm |
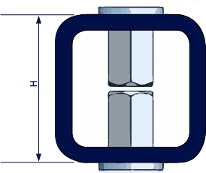
Beispiel - Blindnietmutter
Blindnietmuttern in gegenüberliegenden Seiten | |
---|---|
Typ, Mindesthöhe (H) | |
M4 | 21 mm |
M5 | 27 mm |
M6 | 31 mm | M8 | 35 mm |
Blindnietmuttern in benachbarten Seiten (wenn in der Mitte der Seite platziert) |
|
---|---|
Typ, Mindesthöhe (H) | |
M4 | 28 mm |
M5 | 35 mm |
M6 | 41 mm | M8 | 47 mm |
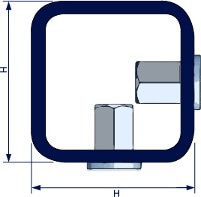
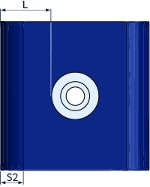
Position des Flansches / Position der Blindnietmutter auf dem Rohr
Typ, Minimum L (mm) | |
M4 | 2 x Wanddicke (S2) |
M5 | 2 x Wanddicke (S2) |
M6 | 2 x Wanddicke (S2) | M8 | 2 x Wanddicke (S2) |
Gewinde & Fließboren
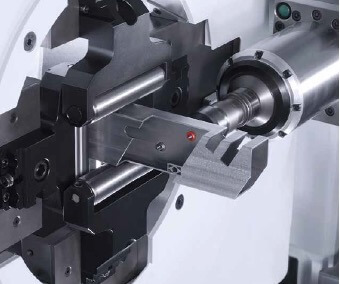
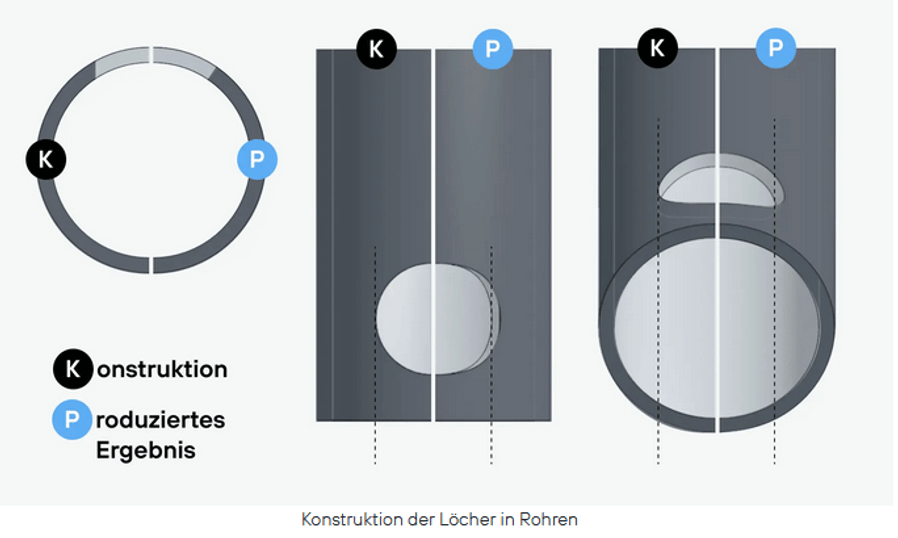
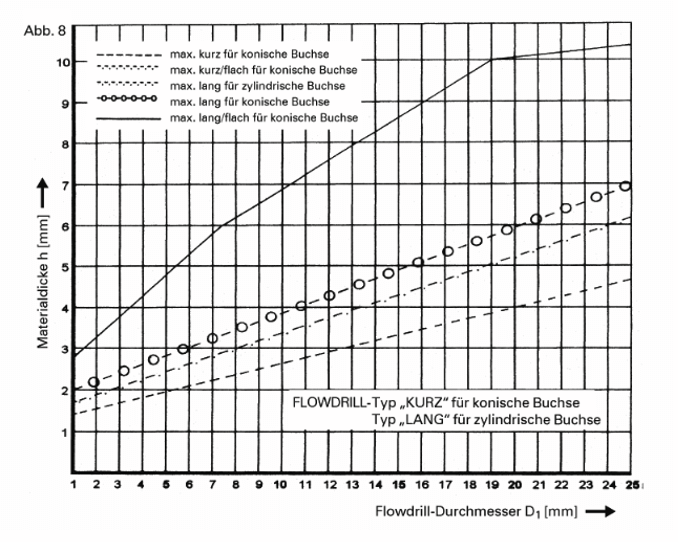
CAD-Vorgaben zur automatischen Erkennung von Gewinden & Flowdrill/Fließbohrungen
Typ | |
M4 | Kernloch Ø3,3 |
M5 | Kernloch Ø4,2 |
M6 | Kernloch Ø5 | M8 | Kernloch Ø6,8 | M10 | Kernloch Ø8,5 | M12 | Kernloch Ø10,2 | M16 | Kernloch Ø14,5 |
Fließbohrungen müssen in Ihrer Form (flach oder mit Bund) angegeben werden.
Anwendungen unterschiedlichster Verbindungen
Fertigungsbedingungen FÜR BIEGE UND KANTTEILEN
Maximale Breite > 2.980 mm
Maximale Blechdicke > 10mm
Maximales Gewicht > 300 kg
Standardtoleranzen für Winkelmaße
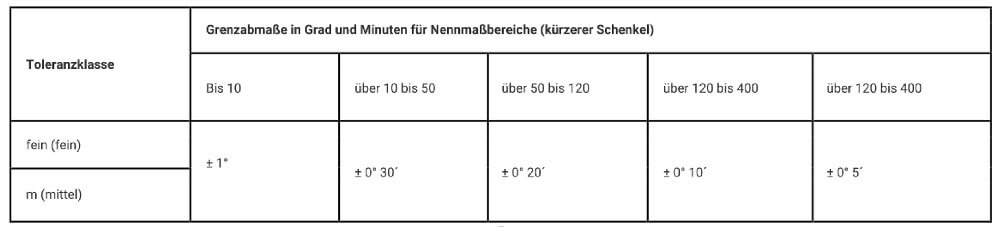
Standardtoleranzen für Längenmaße
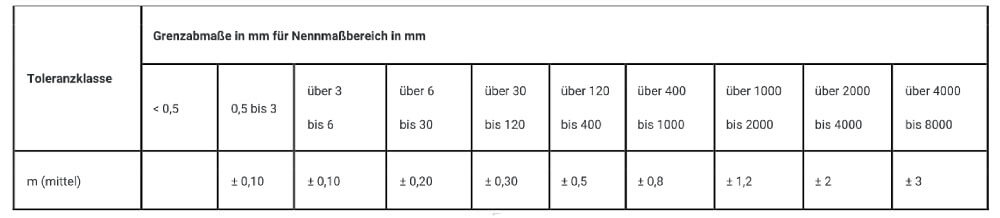
Kantabdrücke
Durch die Biegewerkzeuge bei der Fertigung Kanabdrücke an den Oberflächen der Blechteile entstehen. Zudem kann es beim Biegeprozess zu kleinen Vertiefungen, Kratzer und Rillen kommen. Bitte beachten Sie, dass dies kein Reklamtionsgrund darstellt.
Mindestschenkellängen
Bei der Herstellung von Blechbiegeteilen gibt es werkzeugbedingte Grenzmaße, die schon bei der Konstruktion der Werkstücke zu beachten sind. Liegt eine Seite des Blechteils nicht auf dem Biegewerkzeug auf, ist es nicht möglich die gewünschte Biegung zu erzeugen. Um Herstellbarkeit Ihrer Biegeteile zu gewährleisten, entnehmen Sie bitte die Mindestschenkellängen den untenstehenden Tabellen.
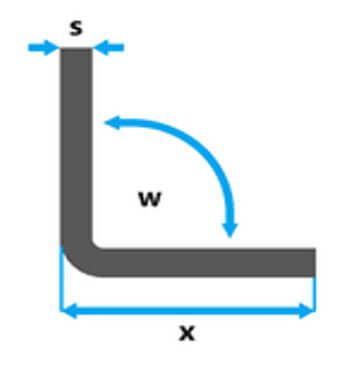
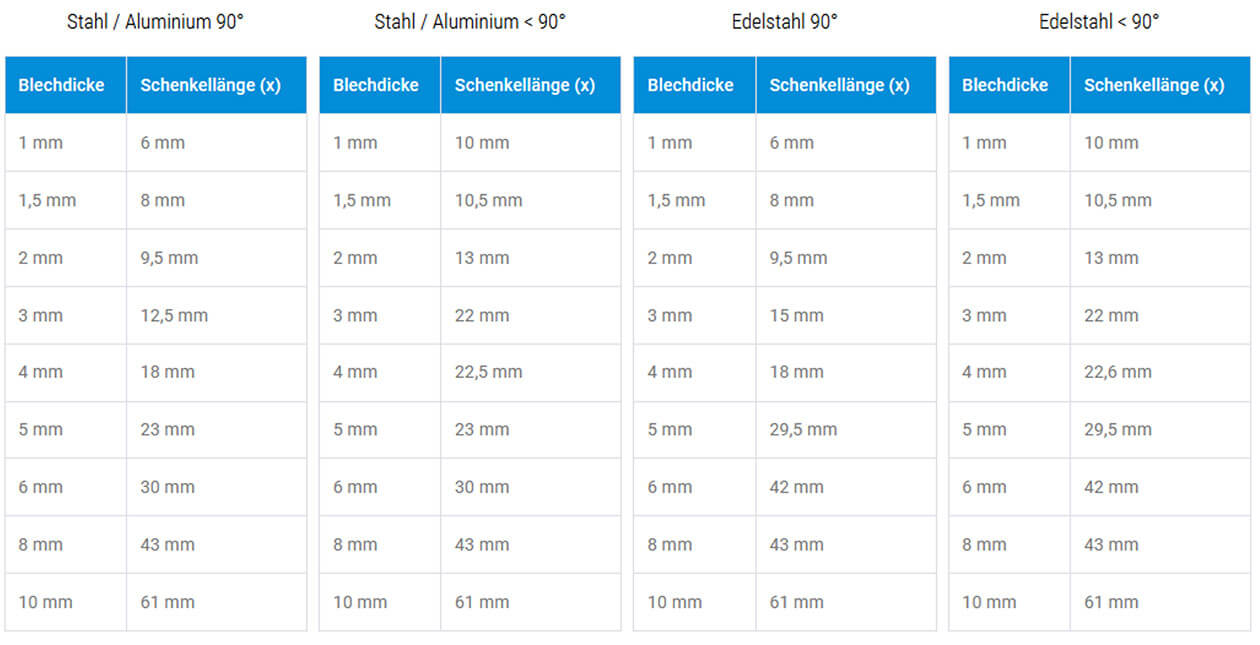
Mindesthöhen bei Z-Biegungen
Bei zwei aufeinanderfolgenden Biegungen (Z-Biegungen) muss fertigungsbedingt eine Mindeststufenhöhe eingehalten werden. Entnehmen Sie bitte die Mindeststufenhöhen den untenstehenden Tabellen, damit die Herstellbarkeit Ihrer Biegeteile gewährleistet ist.
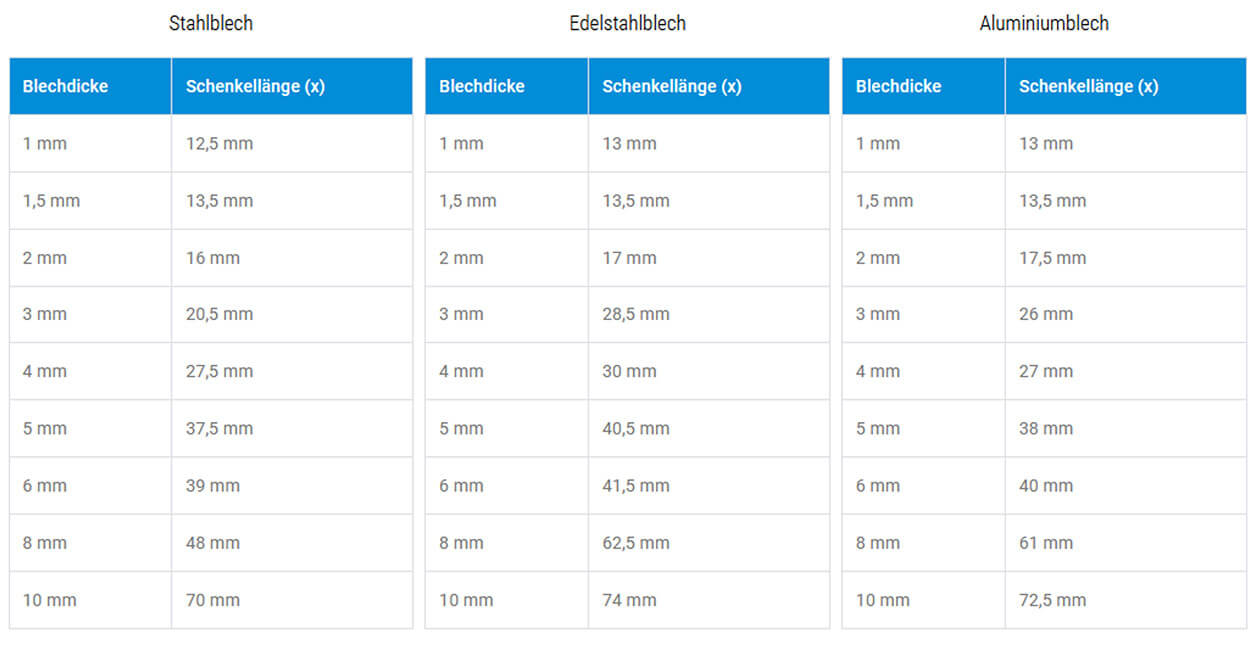
Mindestbiegeradius
Der Mindestbiegeradius definiert den kleinstmöglichen Biegeradius, ohne dass es zum Bruch des Werkstückes kommt. Wie stark eine Blechtafel gebogen werden kann, ist von vielen verschiedenen Faktoren abhängig. Unter anderem spielen der Werkstoff und die Materialdicke dabei eine wichtige Rolle. Wird der Mindestbiegeradius nicht beachtet kann dies zur Rissbildung im Material oder sogar zum Materialbruch führen. Nachdem Sie ihre CAD-Daten hochgeladen haben, wird das Modell von unserem System analysiert und abhängig von Werkstoff und Matrialstärke werden die optimalen Biegewerkzeuge ermittelt. Bitte beachten Sie, dass dadurch die Biegeradien von Ihren Vorgaben abweichen können und dies kein Reklamationsgrund darstellt.
Folgende Mindestbiegeradien sind erforderlich, um eine prozessichere Fertigung zu garantieren:
Aluminium: r = 2 x s
Edelstahl: r = 1 x s
Stahl: r = x s
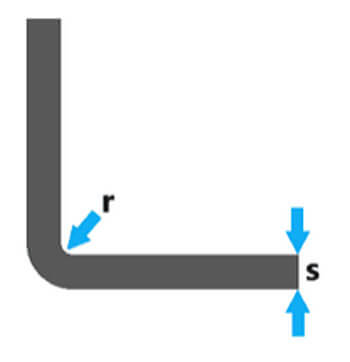
Mindestlochabstand zur Biegung
Löcher und Aussparungen die zu nah an der Biegekante liegen verziehen sich beim Biegen.
Um dies zu vermeiden, empfehlen wir Ihnen den Mindestabstand a = r + 2 x s einzuhalten.
Eine andere "werkstattgerechte" Methoden den Mindestabstand zu ermitteln ist die Verwendung der Mindestschenkellänge. Löcher und Aussparungen die weiter von der Biegelinie entfernt sind als die Mindestschänkellänge sind ohne Verzug herstellbar.
Alternativ können Sie Entlastungsschnitte konstruieren, um Löcher in der Nähe von Biegekanten zu realsieren.
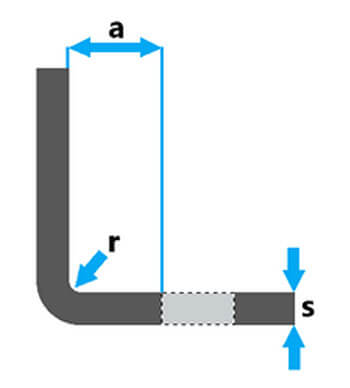
Maximale Schachtelhöhe
Bei Blechteilen die drei oder mehr gekantete Seiten haben kann es zur Kollision mit der Biegemaschine oder den Biegewerkzeugen kommen. Bei Photoncut können Sie solche Schachteln / Kisten bis zu einer maximalen Höhe von 230mm bestellen.
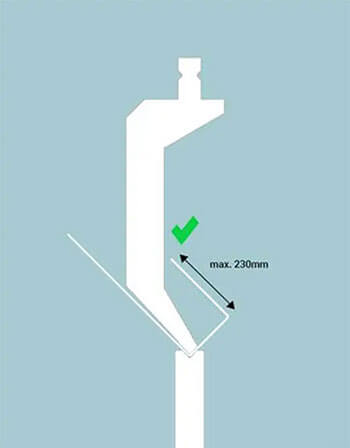
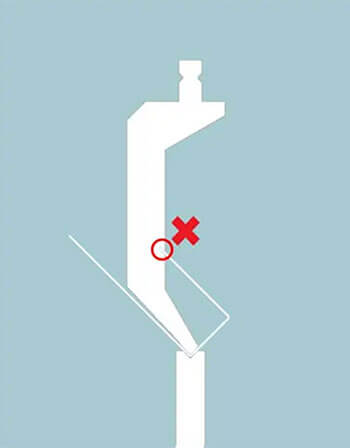
Alternativ kann auch der senkrechte Abstand zur Biegelinie mit Abmessung der Mindestschenkellänge konstruiert werden, damit das gewünschte Biegeergebnis gewährleistet ist.
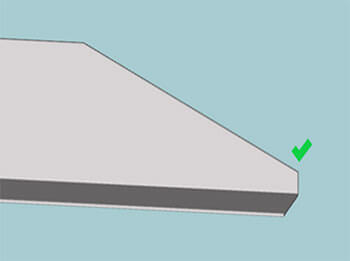
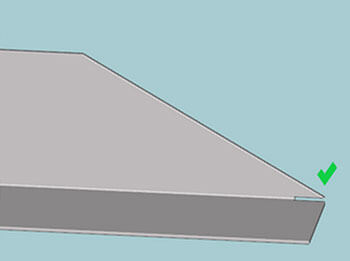
Kollision mit dem Werkzeug
Kisten oder U-Profile mit zu langen Schenkellängen im Verhältnis zur Innenfläche (Basis) können nicht hergestellt werden, da es zur Kollision mit dem Biegewerkzeug oder dem Pressbalken darüber kommt.
Verkürzen Sie wenn möglich einen Schenkel oder verlängern Sie die Basis des U-Profils, damit das Blechteil korrekt gebogen werden kann.
Freischnitte
Wenn der Mindestlochabstand zur Biegung konstruktionsbedingt nicht eingehalten werden kann, können Freischnitte gesetzt werden. Dadurch wird verhindert, dass sich die Löcher und Aussparungen beim Biegen verziehen.
Beim Konstruieren der Freischnitte gilt es folgendes zu beachten:
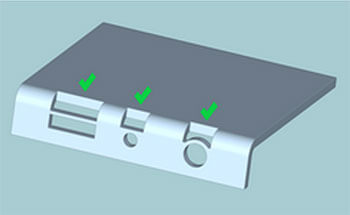
Biegelinien sollten nicht unmittelbar in das Material übergehen, weil die Stauchung und Dehnung in der Biegezone sonst behindert wird und Risse verursacht.
Freistiche zwischen der Biegezone und dem Material minimieren die Kerbwirkung und das Blechteil kann korrekt
gebogen werden.
Beim Aufeinandertreffen von zwei Kantungen (z.B. in einer Ecke) wird ein Eckfreistich benötigt, um das Blechteil herstellen zu können.
Die einfachste Methode hierfür ist es einen Ausschnitt in das Werkstück zu konstruieren.
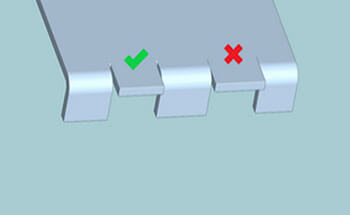
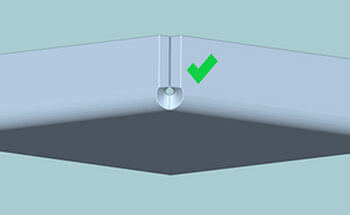
Werkzeugbedingt kann keine homogene Biegung entlang der vorgesehenen Kante hergestellt werden, wenn schräge Kanten zur Biegelinie laufen. Auch hierbei kann ein Freischnitt Abhilfe schaffen.
Gewindebohrungen
Bitte beachten Sie, dass Ihre hochgeladenen CAD-Daten keine Gewindebohrungen enthalten dürfen. Die Dateien dürfen nur die benötigten Kernlöcher enthalten. ACHTUNG!
Der Durchmesser der Kernlochbohrung ist immer kleiner als der spätere Innendurchmesser des Gewindes.
Senkungen
Bitte beachten Sie, dass Ihre hochgeladenen CAD-Daten keine Senkungen enthalten dürfen. Die Dateien dürfen nur die benötigten Kernlöcher enthalten. ACHTUNG! Bei Senkungen im Dünnblech z.B. 1,0 - 2,0 mm ist zu beachten, dass die Senkung den Kernlochdurchmesser vergrößern kann und zudem Abdrücke auf der Unterseite entstehen können.
Maschinelles Entgraten
Maximale Blechteilgröße
> 2.980 mm x 900 mm
Maximale Blechdicke
> 20 mm
Minimale Blechteilgröße
> 150 mm x 50 mm
Unsere Mitarbeiter in der Fertigung entscheiden ie nach Bauteil, ob die Blechteile mittels Durchlaufmaschine oder durch das Bürsten bearbeitet werden. Bitte beachten Sie,
dass beim maschinellen Entgraten Schleifspuren auf der Oberfläche der Werkstücke entstehen und dies kein Reklamationsgrund darstellt.
Fertigungsbedingungen für das Laserschneiden von Blechen
Gratbildung
Bedingt durch Material und Blechdicke können beim Laserschneiden Grate an den Schnittkanten entstehen. Bei uns haben Sie die Möglichkeit diese Grate durch maschinelles Entgraten oder Gleitschleifen/Trowalieren entfernen zu lassen.
Wir empfehlen das zusätzliche Entgraten der Blechteile bei der Konfiguration anzuwählen!
Weitere Informationen hierzu finden Sie unter dem Fertigungsverfahren Entgraten.
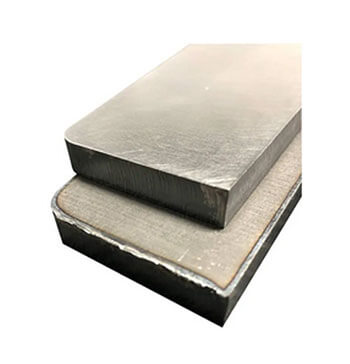
Spritzer
Dass beim Laserschneiden Spritzer entstehen lässt sich oft nicht vermeiden. Metallspritzer auf der Oberfläche und an den Konturen bilden sich durch viele verschiedene Faktoren wie...
- den Werkstoff und die Blechdicke
- die Teilegeometrie
- den Lasereinstich sowie
- die Verschachtelung der Bauteile.
Wir möchten darauf hinweisen, dass durch den Fertigungsprozess entstandene Spritzer in der Regel keinen Reklamationsgrund darstellen. Beim Entgraten der Blechzuschnitte lassen sich diese Spritzer mit wenig Aufwand und geringen Kosten entfernen.
Für Laserzuschnitte die frei von Spritzern sein müssen empfehlen wir Ihnen daher, den zusätzlichen Bearbeitungsschritt „Entgraten" bei der Konfiguration Ihrer Bauteile auszuwählen.
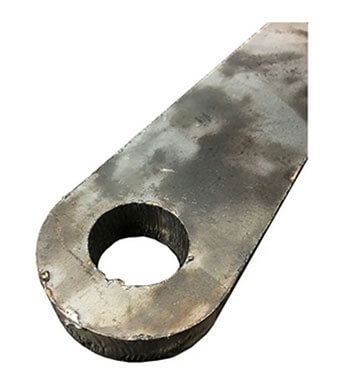
Anlauffarben / Anlassfarben
Beim Laserschneiden kann es abhängig von Werkstoff und Teilekontur zu Verfärbungen kommen. Diese Verfärbungen werden auch Anlauffarben oder Anlassfarben genannt. Besonders kleine Geometrien sowie enge Leisten und Stege begünstigen die Verfärbungen, da hier die Hitze die beim Schneidprozess entsteht nicht entweichen kann. Bitte beachten Sie, dass solche Verfärbungen fertigungsbedingt entstehen und keinen Reklamationsgrund darstellen.
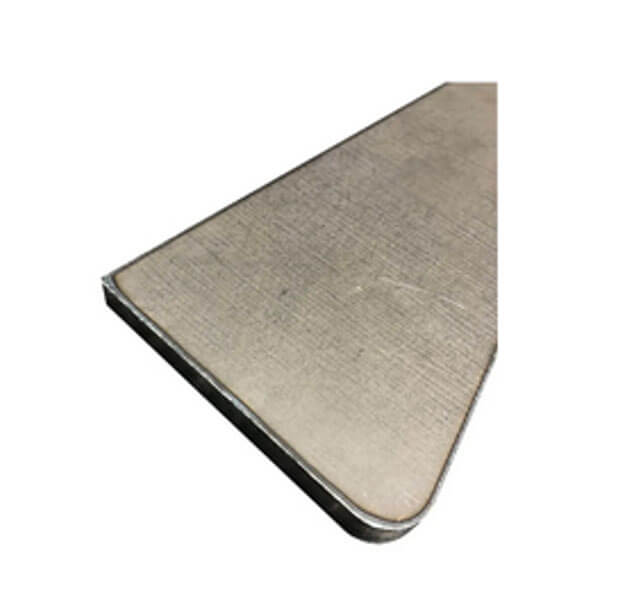
Schnittrillen an der Kontur
Abhängig vom Werkstoff und Blechdicke erhält die Schnittkante ein für das Laserschneiden typisches Rillenmuster. Wir möchten darauf hinweisen, dass dies kein Reklamationsgrund ist Grundsätzlich gilt, je dicker das Material, desto ausgeprägter das Rillenmuster an der Schnittkante. Hier bei einem 20 mm dickem Baustahl zu sehen.
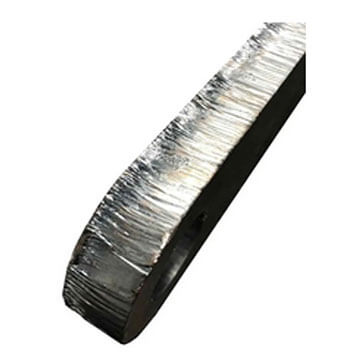
Micro-Ecken
Micro-Ecken sind Stege zwischen dem Werkstück und der Blechtafel, um ein herausfallen, verschieben oder aufstellen der Laserzuschnitte zu verhindern. Besonders bei kleineren Bauteilen ist dies notwendig, da sonst die Gefahr besteht, dass die Teile durch das herunterfallen beschädigt werden oder den Schneidprozess durch kippen/ aufstellen behindern. Bitte beachten Sie, dass Micro-Ecken für einen sicheren Fertigungsprozess notwendig sind und keinen Reklamationsgrund darstellen.

Kleberückstände bei Material mit Schutzfolie
Bitte berücksichtigen Sie, dass es bei Blechtafeln mit Schutzfolie durch die Wärmeeinwirkung beim Laserschneiden und dem damit verbundenen schmelzen der Folie dazu kommen kann, dass sich die Folie entlang der Schnittkontur nur schlecht lösen lässt.
Außerdem kann es zu schwer entfernbaren Kleberesten kommen. Dies ist fertigungsbedingt nicht anders möglich und stellt keinen Reklamationsgrund
"Oxidfreie Kanten"
Wenn Ihre Bauteile Pulverbeschichtet oder Lackiert werden, wählen Sie bitte bei der Materialauswahl einen Werkstoff hinter dem der Zusatz „Oxidfreie Kanten" steht.
Beim Laserschneiden wird dann beim Schneidverfahren das etwas teurere Gas
„Stickstoff" verwendet. Es entsteht somit keine Zunderschicht (Oxidschicht) die sich später ablöst und somit Lackabplatzer verursacht. Bekommen die Teile keine Oberflächenbehandlung, können diese günstiger mit Sauerstoff geschnitten werden.
ANFORDERUNGEN AN LASERTEILE
Die Datei muss enthalten:
- Dateiformat DXF oder STEP
- Zeichnungsmaßstab 1:1
- Eine Zeichnung pro Datei
- Ausschließlich Produktkonturen
- Bei Gewindebohrungen nur Kernlochdurchmesser
- Volllinien
- Teilekonturen in Weiß
- Gravuren in Gelb
- Platinengröße von 10 x 10 mm bis 2980 x 1480 mm
Die Datei darf nicht enthalten:
- Rahmen
- Maßlinine
- Schriftfelder
- Beschriftungen
- Gewindebohrungen
- Senkungen
- Fasen
- Gestrichelte Linien
- Biegelinien
Mindestmaß Löcher
Der Lochdurchmesser muss mindestens der Materialstärke entsprechen
> Mindestens Blechdicke
Löcher, die aufgrund des Durchmessers zu klein sind, werden mit einer Körnung markiert!
Allgemeintoleranzen
DIN ISO 2768-m: Grenzmaße für Längenmaße
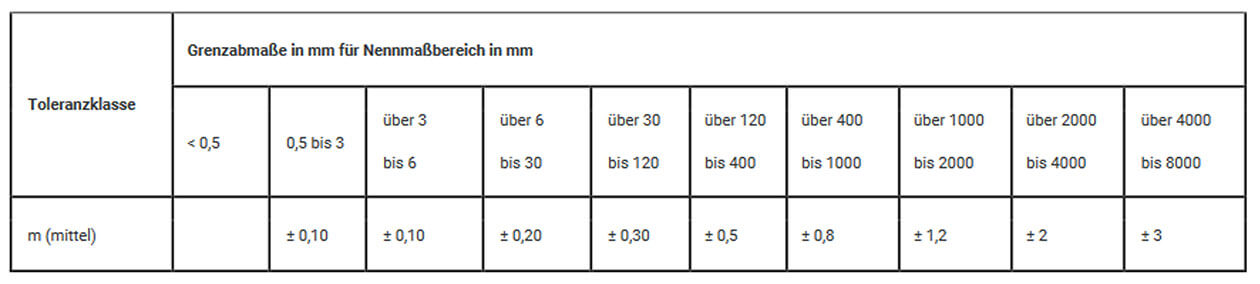
Standardtoleranz für Winkelmaße
DIN ISO 2768-m
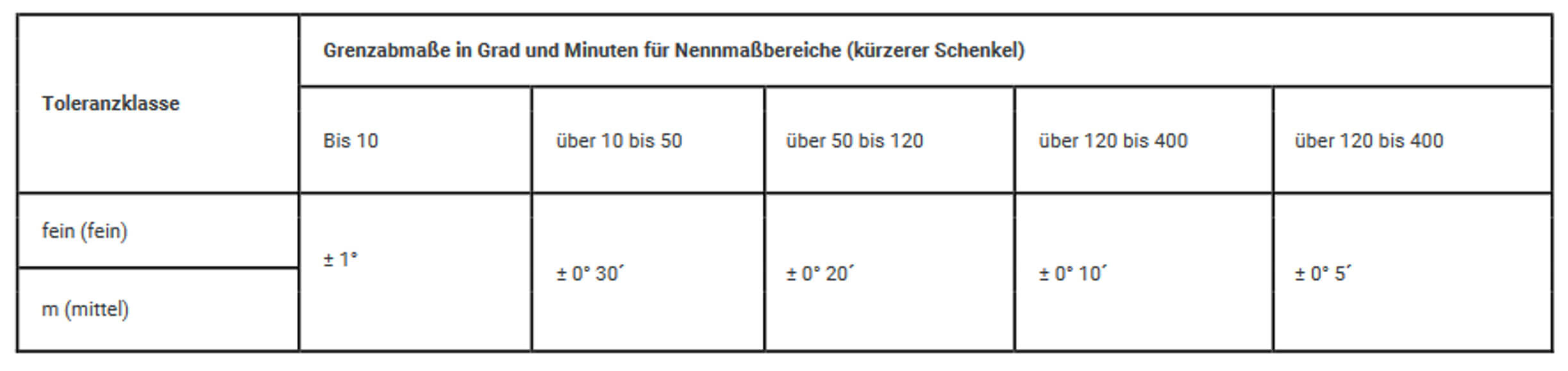
Standardtoleranz bei thermischen Verfahren
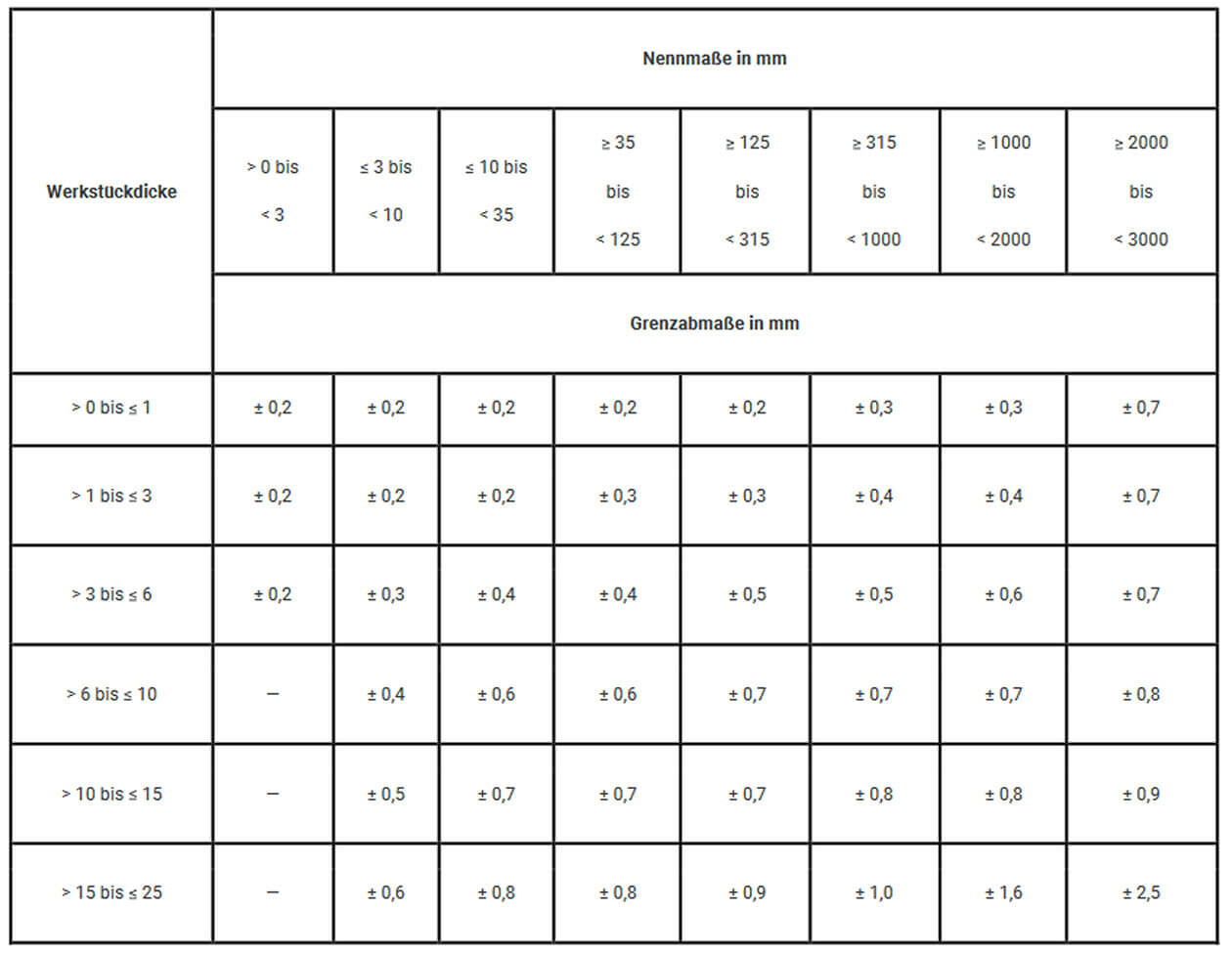
Grenzabmaße für Rundungshalbmesser und Fasenhöhe
DIN ISO 2768-m
